Addressing Challenges In Automated Visual Inspection Of Lyophilized Vials
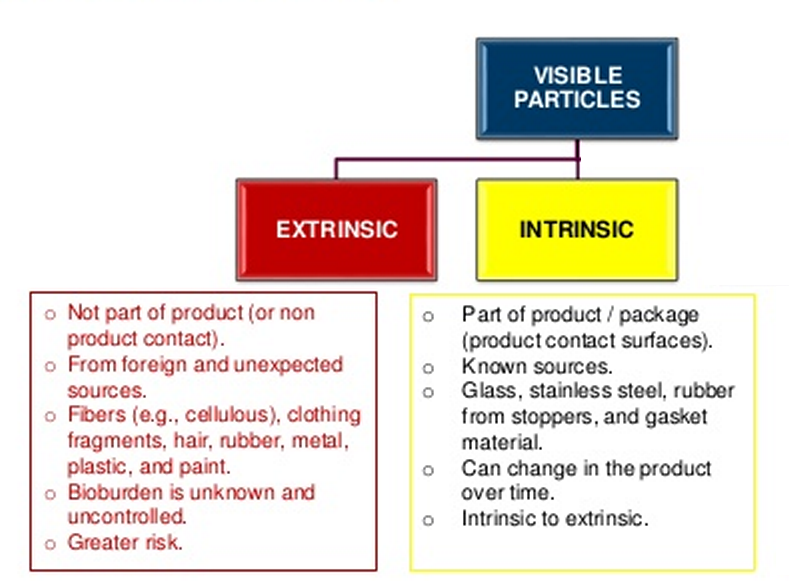
Table of Contents
Overcoming Image Acquisition Challenges in Automated Visual Inspection of Lyophilized Vials
High-quality image acquisition is paramount for successful automated visual inspection. Several challenges need to be addressed to obtain clear, consistent images suitable for accurate defect detection.
Lighting and its Impact on Image Quality
Proper lighting is crucial for capturing subtle defects. Different lighting techniques, each with its advantages and disadvantages, impact image quality.
- Coaxial lighting: Provides uniform illumination, minimizing shadows, but can struggle with highly reflective surfaces.
- Diffuse lighting: Offers soft, even illumination, reducing glare, but might not highlight fine details as effectively.
- Ring light: Provides bright, even illumination, but can create reflections on curved vial surfaces.
The challenge lies in selecting the optimal lighting technique and carefully controlling its intensity to minimize glare and reflections while maximizing defect visibility. Consistent lighting is essential for reliable and repeatable results in automated visual inspection of lyophilized vials.
Camera Selection and Image Resolution
Choosing the right camera is critical for capturing fine details. High-resolution cameras are essential for detecting small defects such as cracks or particulate matter.
- High-resolution cameras: Crucial for capturing fine details and improving defect detection sensitivity.
- CMOS vs. CCD sensors: CMOS sensors offer higher frame rates and lower power consumption, while CCD sensors generally provide better image quality in low-light conditions. The choice depends on the specific application requirements.
- Magnification and field of view: Appropriate magnification is needed to capture sufficient detail, while a suitable field of view ensures efficient inspection of the entire vial surface. Finding the optimal balance is key for efficient automated visual inspection of lyophilized vials.
Dealing with Vial Variations and Orientation
Vials can vary in size, shape, and orientation, posing a challenge for automated systems. Robust image processing algorithms are necessary to handle these variations.
- Varied vial dimensions: Algorithms must adapt to different vial sizes and shapes, ensuring consistent image analysis.
- Random vial orientation: Robotic systems with automated vial handling and orientation capabilities are often necessary to standardize the inspection process.
- Advanced image processing: Robust algorithms are essential to compensate for variations in vial position and lighting conditions, ensuring reliable defect detection in automated visual inspection of lyophilized vials.
Advanced Image Processing and Defect Detection Algorithms for Automated Visual Inspection of Lyophilized Vials
Effective image processing and robust defect detection algorithms are crucial for accurate and reliable results.
Image Segmentation and Preprocessing Techniques
Before defect detection, the vial and its contents must be accurately separated from the background. This requires sophisticated image segmentation techniques.
- Background subtraction: Algorithms to remove background noise and isolate the vial for precise analysis.
- Noise reduction filters: Techniques to eliminate noise and enhance image clarity for improved defect detection.
- Image enhancement: Algorithms to sharpen edges and improve contrast, facilitating accurate segmentation and defect identification in automated visual inspection of lyophilized vials.
Defect Classification and Identification
Automated systems need to reliably classify and identify various defects found in lyophilized vials.
- Defect types: Common defects include cracks, particulate matter, discoloration, and vial imperfections.
- Machine learning algorithms: These algorithms are trained on large datasets of images with labeled defects to classify and identify different defect types with high accuracy.
- Model training and validation: Rigorous training and validation are critical to ensure the accuracy and reliability of the defect detection model for automated visual inspection of lyophilized vials.
False Positive Reduction Strategies
Minimizing false positives is crucial for efficient and reliable inspection. Strategies to reduce false positives include:
- Multi-stage inspection: Employing multiple image analysis techniques to cross-validate results and filter out false positives.
- Rule-based filtering: Implementing rules based on defect characteristics to filter out potential false positives.
- Statistical analysis: Using statistical methods to identify and remove outliers that might be misclassified as defects.
Validation and Regulatory Compliance for Automated Visual Inspection of Lyophilized Vials
Validation and compliance with regulatory requirements are critical for ensuring the reliability and acceptance of automated visual inspection systems.
Meeting Regulatory Requirements
Automated systems must meet stringent regulatory standards to ensure data integrity and product quality.
- FDA and EMA guidelines: Compliance with relevant guidelines is crucial for approval and market access.
- Validation protocols: Comprehensive protocols are needed to demonstrate system performance and reliability.
- Performance qualification: Regular performance checks and system verification are required to maintain compliance and ensure ongoing accuracy.
Data Management and Traceability
Effective data management and traceability are essential for regulatory compliance and quality control.
- Secure data storage: Maintaining secure storage and retrieval of inspection data.
- Audit trails: Generating detailed audit trails to track all system activities and changes.
- Electronic records: Using electronic record-keeping systems to comply with regulatory requirements for data management in automated visual inspection of lyophilized vials.
Conclusion: Optimizing Your Lyophilized Vial Inspection Process with Automation
Implementing Automated Visual Inspection of Lyophilized Vials presents significant challenges, including image acquisition, algorithm development, and regulatory compliance. However, overcoming these obstacles yields substantial benefits, such as increased speed, higher accuracy, improved consistency, and enhanced regulatory compliance. By carefully selecting appropriate hardware, developing robust algorithms, and implementing rigorous validation procedures, pharmaceutical manufacturers can optimize their lyophilized vial inspection processes and ensure consistently high product quality. To learn more about implementing automated visual inspection solutions tailored to your specific needs, contact us today.
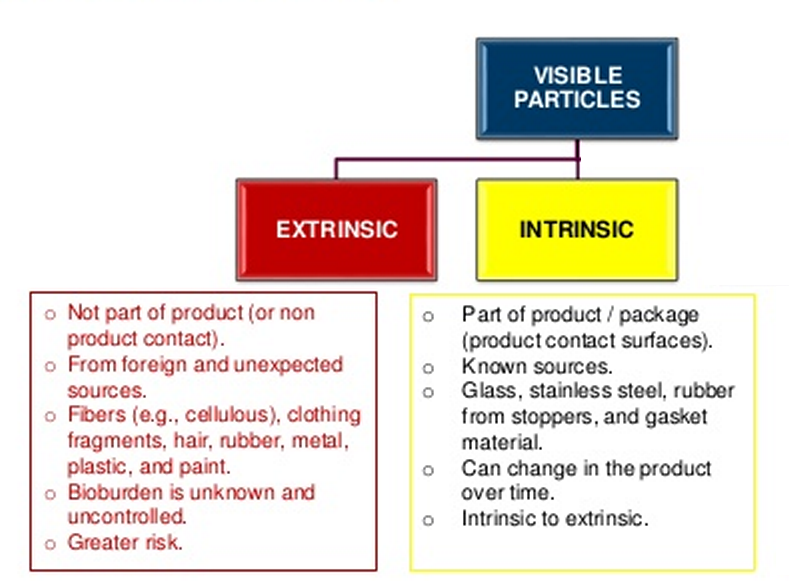
Featured Posts
-
Technical Issue Forces Blue Origin To Postpone Rocket Launch
May 11, 2025 -
Yankees Magazine Examining Aaron Judges Path To A Historic 2024
May 11, 2025 -
Potential Tariffs On Aircraft And Engines Examining Trumps Trade Policy
May 11, 2025 -
Eric Antoine Et Sa Compagne Une Histoire D Amour Discrete
May 11, 2025 -
Kontrowersje Wokol Ksiecia Andrzeja Szokujace Wyznania Masazystki
May 11, 2025
Latest Posts
-
Fotografii S Borisom Dzhonsonom Teper Platnye Chto Izvestno
May 12, 2025 -
Razgovor Putina I Dzhonsona Aktsent Na Rossiyskikh Atomnykh Submarinakh
May 12, 2025 -
Vin Smiyetsya Nad Nami Reaktsiya Borisa Dzhonsona Na Rozmovu Putina Ta Trampa
May 12, 2025 -
Boris Johnsons Most Awkward Animal Encounters From Dog To Ostrich
May 12, 2025 -
Skolko Zarabatyvaet Boris Dzhonson Na Selfi
May 12, 2025