Automated Visual Inspection Of Lyophilized Vials: A Comprehensive Analysis Of Challenges
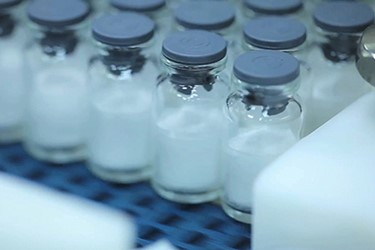
Table of Contents
Challenges in Image Acquisition for Automated Visual Inspection of Lyophilized Vials
Achieving reliable automated inspection of lyophilized vials begins with acquiring high-quality images. However, several factors contribute to significant challenges in this process.
Lighting and Illumination Issues
Consistent and optimal illumination is crucial for accurate defect detection. However, variations in several aspects make this challenging:
- Vial Transparency: Differences in glass clarity and thickness can affect light transmission, leading to uneven illumination.
- Surface Reflections: The curved surface of vials can cause reflections that obscure the lyophilized cake, creating false positives or masking defects.
- Shadowing Effects: The shape of the vial and the cake itself can create shadows, hindering the detection of subtle defects.
- Lighting Source Variations: Different lighting sources (LED, halogen) produce varying spectral characteristics, potentially impacting image quality and consistency.
These illumination inconsistencies can lead to significant errors in automated defect detection. To mitigate these issues, techniques like diffused lighting and polarization are often employed to improve image uniformity and reduce reflections.
Variations in Vial Geometry and Fill Levels
Inconsistencies in vial shape, size, and fill levels further complicate automated visual inspection.
- Standardizing Image Acquisition: Adapting image acquisition parameters to account for variations in vial geometry and fill levels is difficult.
- Cake Appearance Variations: The appearance of the lyophilized cake itself varies, with cracks, collapse, and other variations in texture posing challenges for automated systems.
- Detecting Small Defects: Identifying small defects against a varied background is especially difficult when the cake's appearance changes from vial to vial.
These variations demand adaptive image processing algorithms capable of handling the inherent inconsistencies in vial presentation. Advanced algorithms must account for these differences to ensure consistent and reliable inspection results.
Algorithm Development and Implementation Challenges
Even with high-quality images, developing effective algorithms for automated inspection presents considerable hurdles.
Defect Detection and Classification
Accurately identifying and classifying defects is a complex task.
- Differentiating Acceptable Variations from Defects: Distinguishing between acceptable variations in cake appearance and actual defects requires sophisticated algorithms.
- Detecting Subtle Defects: Identifying micro-cracks, particulate matter, and other subtle defects demands high resolution and advanced image analysis techniques.
- Balancing False Positives and Negatives: Minimizing both false positives (rejecting acceptable vials) and false negatives (accepting defective vials) is crucial.
Sophisticated image analysis techniques, such as machine learning and deep learning, are essential for this task. However, the effectiveness of these algorithms is heavily reliant on the quality and size of the training datasets.
Integration with Existing Manufacturing Lines
Integrating automated inspection systems into existing pharmaceutical production lines poses significant practical challenges.
- Equipment Compatibility: The automated system must seamlessly integrate with existing filling, capping, and other production equipment.
- Throughput Requirements: The system needs to meet the required throughput of the manufacturing line without causing bottlenecks.
- Validation and Regulatory Compliance: Rigorous validation and compliance with regulatory guidelines (e.g., GMP) are essential.
- Cost of Implementation: The high initial investment cost needs to be justified by improved quality and efficiency.
Careful consideration of these factors is crucial to ensure successful integration and maximize the return on investment.
Regulatory Compliance and Validation Requirements
The pharmaceutical industry is heavily regulated, and automated visual inspection systems must meet stringent requirements.
Meeting Regulatory Standards
Compliance with regulatory standards is paramount for automated lyophilized vial inspection systems.
- Validation Requirements (IQ, OQ, PQ): Installation Qualification (IQ), Operational Qualification (OQ), and Performance Qualification (PQ) are required to demonstrate system functionality and reliability.
- Data Integrity: Maintaining the integrity of all inspection data is crucial for traceability and regulatory compliance.
- Traceability: A complete audit trail must be maintained for all inspections, ensuring full traceability of results.
- GMP Compliance: Adherence to Good Manufacturing Practices (GMP) guidelines is essential.
Thorough documentation, rigorous testing, and ongoing system maintenance are necessary to ensure continuous compliance.
Data Management and Reporting
Automated systems generate large amounts of data, requiring robust data management strategies.
- Data Storage: Secure and efficient storage solutions are needed to manage the volume of data generated.
- Data Security: Protecting data integrity and confidentiality is paramount.
- Report Generation: Automated report generation is crucial for efficient quality control and regulatory reporting.
- Integration with Other Systems: Integration with laboratory information management systems (LIMS) and manufacturing execution systems (MES) is often necessary.
Robust data management practices are essential for ensuring traceability and effective quality control.
Conclusion
Automated visual inspection of lyophilized vials presents numerous challenges, encompassing image acquisition, algorithm development, system integration, and regulatory compliance. Overcoming these challenges requires a multi-faceted approach, encompassing advanced imaging techniques, sophisticated algorithms, careful system integration, and rigorous validation. By addressing these complexities, the pharmaceutical industry can achieve more robust quality control, enhance product safety, and improve overall manufacturing efficiency. Investing in advanced solutions for automated lyophilized vial inspection is crucial for maintaining competitiveness and ensuring compliance in today's demanding regulatory environment. Explore the latest advancements in automated inspection of lyophilized products to optimize your quality control processes and improve your manufacturing operations.
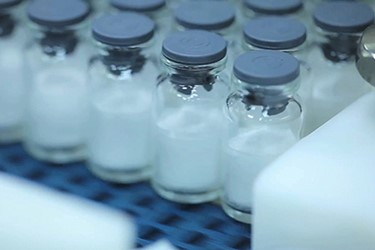
Featured Posts
-
Tasman Council Urged Be Realistic About Keeping Key Road Open For Truckers
May 12, 2025 -
New Calvin Klein Campaign Featuring Lily Collins Photo Gallery
May 12, 2025 -
Shane Lowry Divided American Opinions After Viral Video
May 12, 2025 -
Latest John Wick 5 News A Thrilling Update And Release Date Mystery
May 12, 2025 -
Nine Possible Successors To Pope Francis Leading Cardinal Candidates
May 12, 2025
Latest Posts
-
Increased Border Checks Lead To Fewer Arrests More Deportations
May 12, 2025 -
Asylum Policy Under Fire Ministers Dismissal Of Inspectorate Opinion
May 12, 2025 -
Fewer Arrested More Turned Away The Rise Of Stricter Border Controls
May 12, 2025 -
Controversy Asylum Minister Bypasses Legal Advice From Inspectorate
May 12, 2025 -
Asylum Seeker Claims Exemption From Inspectorates Legal Opinion
May 12, 2025