Electric Vehicle Battery Manufacturing: A Case Study Addendum On BYD's Leadership
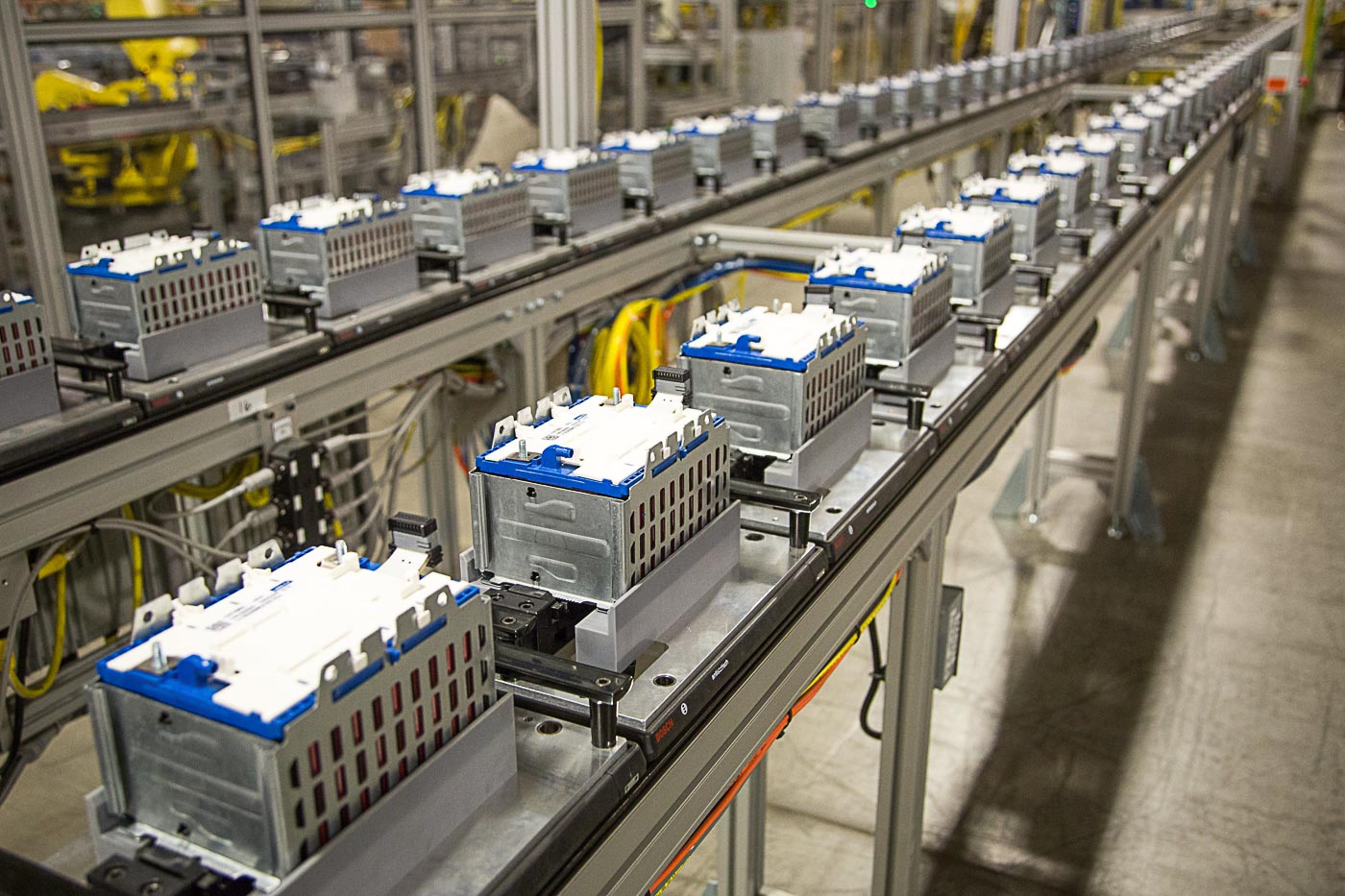
Table of Contents
BYD's Vertical Integration Strategy in Electric Vehicle Battery Manufacturing
BYD's success in electric vehicle battery manufacturing stems significantly from its vertically integrated business model. This strategy grants them unparalleled control over the entire process, from raw material sourcing to final vehicle assembly.
Blade Battery Technology and its Advantages
BYD's Blade Battery is a game-changer in the EV battery landscape. Its unique design, utilizing lithium iron phosphate (LFP) chemistry and a blade-like form factor, offers several key advantages:
- Increased Energy Density: The Blade Battery boasts a higher energy density compared to traditional LFP batteries, resulting in extended driving range for EVs. Independent tests have shown improvements of up to 50% compared to some competitors.
- Improved Safety: The Blade Battery's design minimizes the risk of thermal runaway, a significant safety concern with some battery chemistries. Its robust structure and inherent properties contribute to enhanced safety features.
- Reduced Manufacturing Costs: BYD's efficient manufacturing process and optimized design lead to lower production costs, contributing to more affordable EVs.
Compared to other battery technologies like Nickel Manganese Cobalt (NMC) batteries, the Blade Battery offers a compelling combination of safety, cost-effectiveness, and sufficient energy density for a wide range of EV applications. While NMC batteries may offer slightly higher energy density in some cases, the safety and cost advantages of the Blade Battery make it a strong contender. This translates to improved EV range and faster charging times, making them more attractive to consumers. For instance, BYD's Atto 3 boasts a significant range on a single charge thanks to this technology.
Control over the Entire Supply Chain
BYD's vertical integration extends across the entire EV battery supply chain:
- Raw Material Sourcing: BYD invests heavily in securing raw materials, including lithium, cobalt, and manganese, reducing dependence on external suppliers and ensuring a consistent supply. This includes significant investments in mining and processing operations.
- Cell Production: BYD manufactures its own battery cells, providing precise quality control and enabling rapid innovation.
- Battery Pack Assembly: The company assembles its battery packs in-house, further enhancing control over the final product's quality and performance.
- Vehicle Manufacturing: BYD's control extends to vehicle manufacturing, optimizing battery integration and overall vehicle design.
This vertical integration offers several benefits:
- Cost Reduction: Eliminating intermediary costs and optimizing production processes translates to significant cost savings.
- Quality Control: Maintaining stringent quality standards throughout the entire process guarantees a consistent and high-quality product.
- Faster Innovation Cycles: The ability to rapidly test and implement new technologies within a controlled environment accelerates innovation.
However, this model also presents challenges:
- Potential Bottlenecks: Disruptions in any part of the supply chain can impact the entire operation.
- Vulnerability to Disruptions: External factors such as geopolitical instability or natural disasters can affect raw material availability.
Despite these challenges, BYD's vertical integration strategy has proven highly effective in establishing its leadership in electric vehicle battery manufacturing.
Sustainable Practices in BYD's Electric Vehicle Battery Manufacturing
BYD is committed to environmentally responsible electric vehicle battery manufacturing, integrating sustainability throughout its operations.
Focus on Environmentally Friendly Materials and Processes
BYD actively works to minimize its environmental impact:
- Reduced Carbon Footprint: The company is implementing energy-efficient manufacturing processes and utilizing renewable energy sources in its facilities to reduce its carbon footprint.
- Recycled Materials: BYD incorporates recycled materials wherever possible in its battery production, minimizing waste and resource depletion.
- Environmental Certifications: BYD actively pursues and obtains relevant environmental certifications, demonstrating its commitment to sustainability.
- Lifecycle Assessment: BYD conducts lifecycle assessments of its batteries to identify and minimize environmental impacts throughout their entire lifespan, from raw material extraction to end-of-life disposal.
Battery Recycling Initiatives
BYD recognizes the critical importance of responsible battery disposal and resource recovery:
- Recycling Programs: The company has established comprehensive battery recycling programs to recover valuable materials from end-of-life batteries.
- Resource Recovery: These programs focus on recovering critical materials like lithium, cobalt, and nickel, reducing the need for mining new resources.
- Economic and Environmental Benefits: Battery recycling reduces environmental pollution and offers economic advantages through the reuse of valuable materials.
- Industry Standards: BYD's recycling efforts are setting a high benchmark for the industry, pushing for more sustainable practices across the EV battery sector.
Innovation and Future Outlook for BYD in Electric Vehicle Battery Manufacturing
BYD's continued leadership relies on its commitment to innovation and research and development.
Research and Development Investments
BYD invests significantly in R&D to enhance its battery technology:
- Improved Energy Density: Ongoing research focuses on increasing energy density to further extend EV range.
- Extended Lifespan: BYD is working to improve battery lifespan and durability, reducing the need for frequent replacements.
- Next-Generation Chemistries: The company is exploring next-generation battery chemistries, such as solid-state batteries, to further enhance performance and safety.
- Collaborations: BYD collaborates with research institutions and other companies to accelerate innovation and knowledge sharing.
Global Expansion and Market Share
BYD's global reach is expanding rapidly:
- Global Presence: The company is establishing manufacturing facilities and partnerships worldwide to meet growing global demand for EV batteries.
- Market Share: BYD is steadily increasing its market share in the EV battery sector, becoming a major player on the global stage.
- Market Penetration: BYD employs various strategies to penetrate new markets, including strategic partnerships, direct sales, and targeted marketing campaigns.
- Market Forecasts: Industry analysts predict continued strong growth for BYD, driven by its innovative technologies and aggressive expansion strategy.
Conclusion:
BYD's leadership in electric vehicle battery manufacturing is undeniable, driven by its vertical integration strategy, commitment to sustainability, and continuous innovation. Its Blade Battery technology represents a significant advancement, contributing to improved EV performance and affordability. By controlling its supply chain and investing heavily in R&D and sustainable practices, BYD is setting a new standard for the industry. The future of electric vehicle battery manufacturing will likely be shaped by companies like BYD, demonstrating a clear pathway toward a more sustainable and efficient EV ecosystem. To stay informed on the latest developments in electric vehicle battery manufacturing, continue to follow industry news and analyze the strategies of leading innovators like BYD.
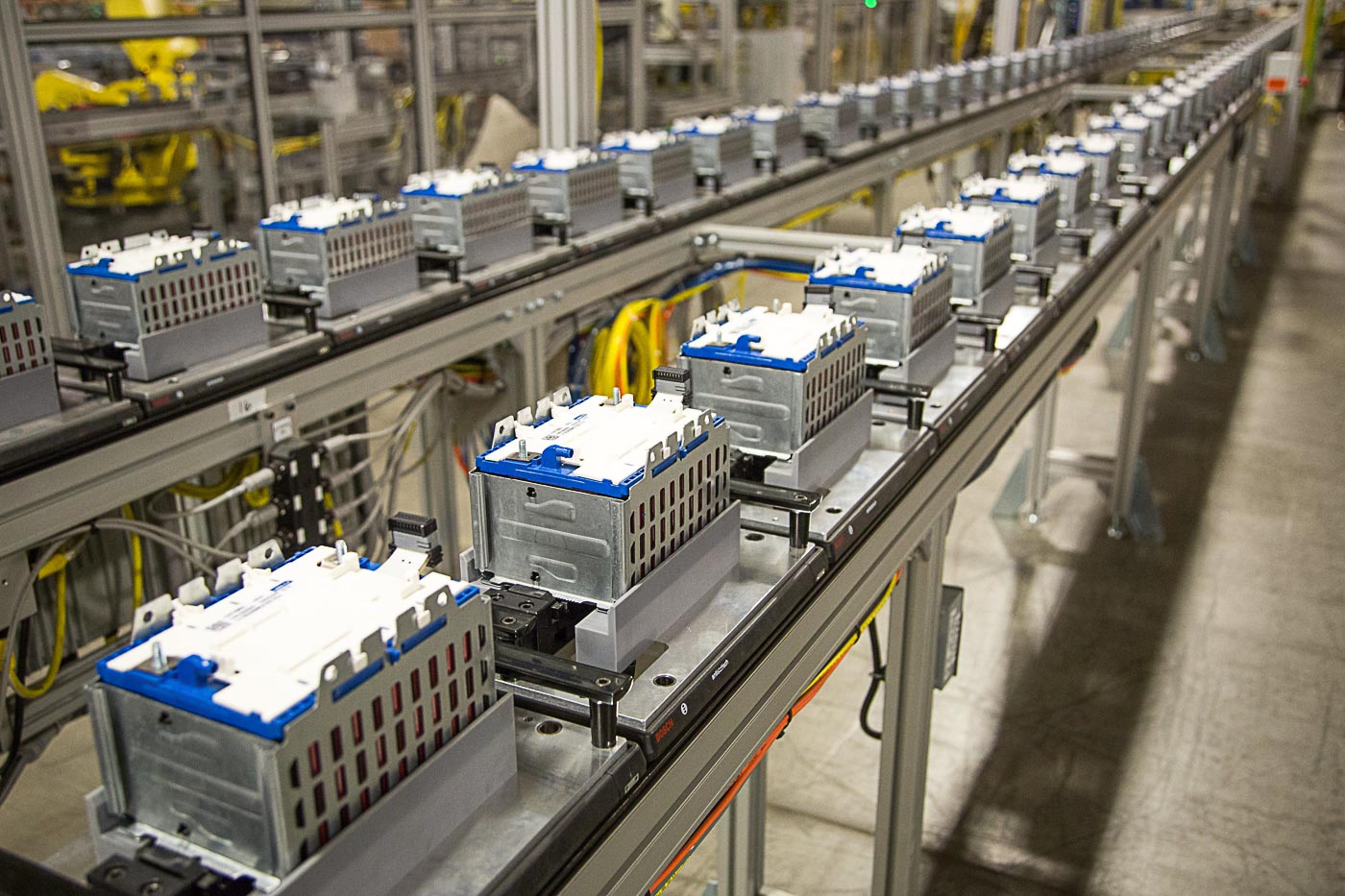
Featured Posts
-
The New Workplace Reality Are Employees Truly Replaceable
May 13, 2025 -
Kemenangan Telak Persipura Jayapura Atas Rans Fc 8 0 Di Playoff Liga 2
May 13, 2025 -
Efl Highlights Your Guide To The Best English Football League Moments
May 13, 2025 -
5 1 Filmes Szerelmespar Akik Valojaban Nem Birtak Egymast Leonardo Di Caprio Es A Toebbiek
May 13, 2025 -
Analyze Mlb Home Run Props Today April 26th Focus On Kyle Tuckers Potential
May 13, 2025