Improving The Accuracy Of Automated Visual Inspection Systems For Lyophilized Vials
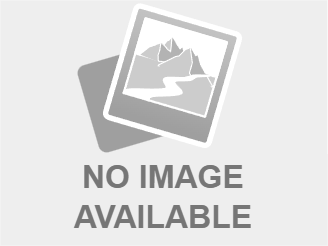
Table of Contents
Optimizing Image Acquisition for Improved Defect Detection
High-quality image acquisition is the foundation of accurate automated visual inspection. Several factors significantly influence the system's ability to detect defects in lyophilized vials.
Illumination Techniques
Proper lighting is crucial. Different lighting techniques offer unique advantages:
- Coaxial illumination: Minimizes shadows, ideal for detecting surface imperfections like scratches and particulate matter. This technique provides a direct, even light source, reducing the obscuring effects of shadows on subtle surface defects.
- Diffuse illumination: Provides even lighting across the vial's surface, suitable for detecting subtle color variations or inconsistencies in the lyophilized cake. This is particularly useful for identifying variations in the cake's appearance that might indicate inconsistencies in the freeze-drying process.
- Structured light: Projects patterns onto the vial's surface, enhancing depth perception and assisting in the detection of cracks, delamination, or inconsistencies in the vial's shape. This advanced technique allows for 3D imaging and analysis, revealing defects not visible with simpler lighting methods.
Camera Selection and Resolution
Camera selection directly impacts the system's sensitivity.
- Sensor size: Larger sensors gather more light, improving image quality, especially in low-light conditions. This is vital for capturing fine details in lyophilized vials.
- Pixel density: Higher pixel density (resolution) allows for the detection of smaller particles and subtle defects, increasing the system's overall accuracy. A high-resolution camera ensures that even minute imperfections are captured clearly.
- Sensitivity: A camera with high sensitivity captures images effectively even in low-light conditions, crucial for maintaining consistent performance across varying lighting conditions. This avoids under-exposed images that might obscure defects.
Image Preprocessing Techniques
Preprocessing enhances the raw images before defect detection.
- Noise reduction: Minimizes false positives caused by image noise. Noise reduction algorithms filter out random variations in pixel intensity, improving the clarity of the image and reducing misidentification of defects.
- Image enhancement: Improves contrast and sharpness, making defects more visible to the algorithm. Techniques like sharpening and contrast stretching enhance the visibility of defects, particularly those that are subtle or difficult to discern.
Advanced Algorithm Development for Defect Classification
Sophisticated algorithms are crucial for accurate defect classification in automated visual inspection systems.
Machine Learning Algorithms
Advanced machine learning provides superior accuracy.
- Deep learning: Deep learning models, trained on extensive datasets of images, can identify a broader range of defects with higher accuracy and can adapt to variations in defect appearance. These models learn complex features from large amounts of training data, allowing them to detect even unseen defects.
- Convolutional Neural Networks (CNNs): CNNs excel at identifying spatial patterns in images, ideal for detecting defects within the context of the lyophilized vial. Their ability to process images in a spatially aware manner is vital for identifying defects based on their shape, size, and location.
Defect Classification and Data Analysis
Effective data analysis is crucial for continuous improvement.
- Statistical Process Control (SPC): SPC charts monitor defect rates over time, allowing for early identification of potential problems and timely corrective actions. Real-time monitoring using SPC ensures efficient process control.
- Data visualization: Data visualization techniques, such as heatmaps or scatter plots, help identify patterns in defect distribution, pinpointing areas needing improvement in the manufacturing process. These techniques help to identify trends in defect types and their frequency, which can then be used to improve the system and process.
False Positive and False Negative Reduction
Minimizing errors is paramount.
- Regular retraining: Regularly retraining and updating machine learning models with new data is crucial for maintaining accuracy and adapting to changing conditions. This ensures that the system is constantly learning and adapting, which is important given the changing nature of pharmaceutical manufacturing.
- Careful algorithm optimization: Careful selection of features and thresholds in algorithms balances sensitivity (detecting all defects) and specificity (avoiding false positives). This ensures that the system is not overly sensitive or not sensitive enough.
System Calibration and Validation for Reliable Performance
Consistent performance is maintained through regular calibration and validation.
Regular Calibration
Calibration ensures the system's accuracy over time.
- Defined schedule: Calibration should follow a defined schedule and documented procedures, ensuring consistent accuracy and reliability over time.
- Traceable standards: Using traceable standards ensures the reliability of the calibration process and meets regulatory requirements.
Validation and Qualification
Validation demonstrates the system's suitability for its intended use.
- Performance verification: Validation protocols verify the accuracy, precision, and sensitivity of the system, ensuring it meets its specified performance requirements.
- Regulatory compliance: Documentation of all validation activities is essential for regulatory compliance.
Conclusion
Improving the accuracy of automated visual inspection systems for lyophilized vials is crucial for maintaining product quality and patient safety. By optimizing image acquisition, employing advanced algorithms, and implementing rigorous calibration and validation procedures, the pharmaceutical industry can significantly enhance the reliability and efficiency of its quality control processes. Investing in state-of-the-art automated visual inspection systems and their ongoing optimization is crucial for maintaining high-quality standards in lyophilized vial production. Regularly reviewing and improving your automated visual inspection systems for lyophilized vials will ensure consistent, high-quality product delivery.
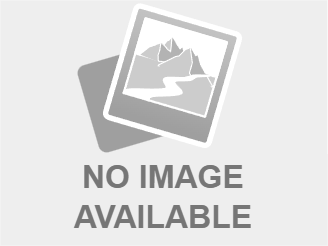
Featured Posts
-
Senior Trips Activities And Events Calendar 2024
May 11, 2025 -
Grand Slam Track League Details And Impact On Global Athletics
May 11, 2025 -
Alex Winters Pre Freaked Mtv Sketch Comedy A Look Back
May 11, 2025 -
Analyzing The Yankees And Rays Injured Lists Ahead Of The May 2 4 Series
May 11, 2025 -
John Wick 5 Confirmed Will Keanu Reeves Return For A Final Showdown
May 11, 2025
Latest Posts
-
Fotografii S Borisom Dzhonsonom Teper Platnye Chto Izvestno
May 12, 2025 -
Razgovor Putina I Dzhonsona Aktsent Na Rossiyskikh Atomnykh Submarinakh
May 12, 2025 -
Vin Smiyetsya Nad Nami Reaktsiya Borisa Dzhonsona Na Rozmovu Putina Ta Trampa
May 12, 2025 -
Boris Johnsons Most Awkward Animal Encounters From Dog To Ostrich
May 12, 2025 -
Skolko Zarabatyvaet Boris Dzhonson Na Selfi
May 12, 2025