Overcoming Hurdles In Automated Visual Inspection Of Lyophilized Drug Products
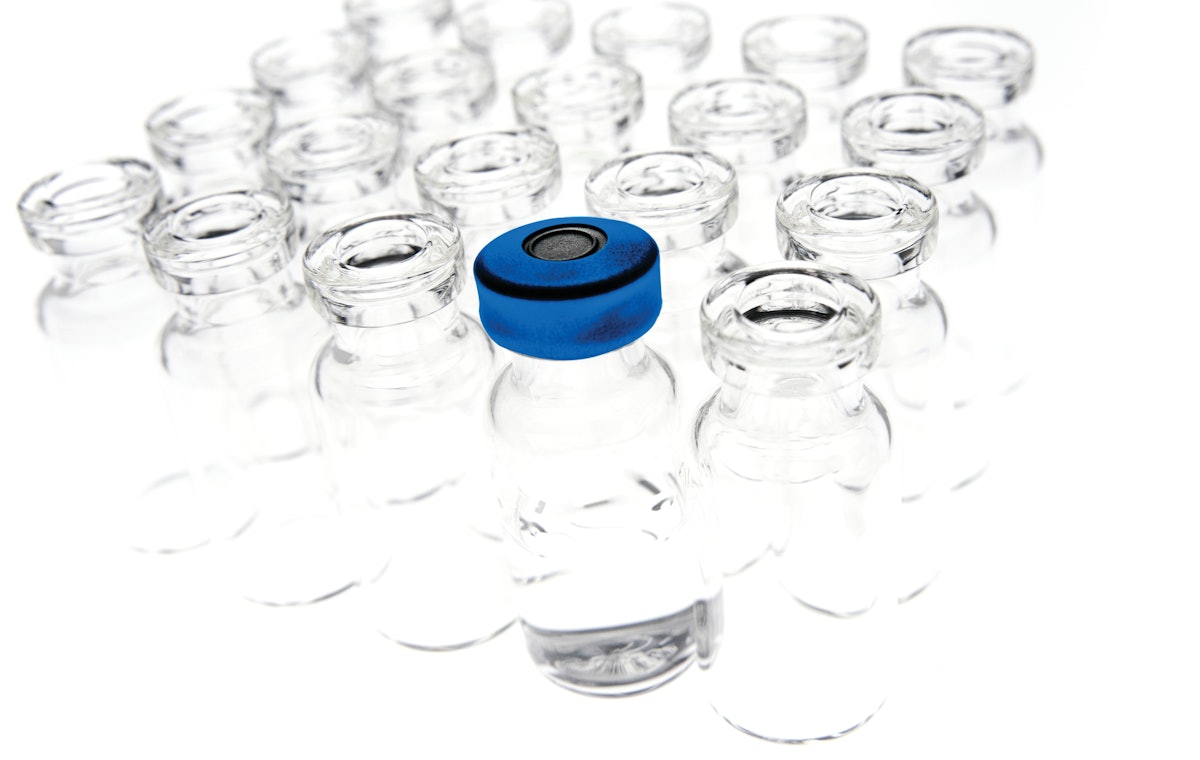
Table of Contents
Challenges in Image Acquisition for Lyophilized Drug Products
Lyophilized drug products, with their unique physical characteristics, present significant challenges to automated visual inspection. The inherent variability in the manufacturing process, coupled with the subtle nature of many defects, necessitates advanced imaging techniques and careful consideration of several key factors.
Variations in Lyophilization Processes
Different lyophilization cycles, even within the same product, can lead to significant variations in cake appearance, making consistent image analysis incredibly difficult. These variations stem from subtle differences in the freezing, primary drying, and secondary drying phases.
- Variations in cake texture: The final product can exhibit differences in porosity, density, and overall structural integrity.
- Color variations: Subtle changes in color can occur due to variations in the lyophilization process or the inherent properties of the drug substance.
- Sublimation patterns: Uneven sublimation can lead to variations in the cake surface, potentially masking or mimicking defects.
- Difficulty in establishing consistent lighting and image capture parameters: Maintaining consistent lighting and camera settings across different batches is essential for reliable image analysis, yet challenging due to variations in cake appearance. Careful calibration and standardization are crucial.
Subtle Defects and High Resolution Needs
Identifying hairline cracks, small particulate matter, or variations in fill level often requires extremely high-resolution imaging capabilities far exceeding those typically used in other pharmaceutical inspection applications. These subtle defects can significantly impact product quality and patient safety, demanding advanced detection methodologies.
- Need for advanced imaging technologies: High-resolution cameras, coupled with specialized lighting techniques such as structured light illumination, are often necessary to capture the fine details required for accurate defect detection.
- Importance of image pre-processing: Advanced image pre-processing techniques, including noise reduction and image enhancement algorithms, are critical for improving the signal-to-noise ratio and enhancing the visibility of subtle defects.
Transparency and Translucency Issues
The inherent properties of some lyophilized products, such as transparency or translucency, can make certain defects extremely difficult to detect. This requires sophisticated algorithms capable of handling variable light transmission characteristics.
- Challenges in differentiating between acceptable variations and actual defects: Distinguishing between inherent variations in the lyophilized cake and actual defects requires advanced image analysis capabilities.
- Necessity of sophisticated image analysis algorithms: Algorithms capable of handling variable transparency and accurately identifying defects despite these variations are essential for reliable automated visual inspection.
Advanced Image Processing and Algorithm Development
The successful implementation of automated visual inspection for lyophilized drug products hinges on the development and deployment of robust image processing and analysis algorithms. This requires expertise in machine learning, computer vision, and statistical process control.
Developing Robust Algorithms for Defect Detection
Designing algorithms that can accurately identify and classify defects requires training on large, diverse datasets of both defective and non-defective products. The algorithms must be robust enough to handle the variations in lighting, background conditions, and cake appearance encountered in real-world scenarios.
- Training algorithms on large, diverse datasets: A comprehensive dataset representing the full range of variations in lyophilized product appearance is essential for accurate algorithm training.
- Addressing the challenges of variations in lighting and background conditions: Algorithms must be insensitive to variations in lighting and background, ensuring consistent performance across different batches and environments.
- Using advanced algorithms like deep learning: Deep learning techniques, such as convolutional neural networks (CNNs), offer significant advantages in handling complex image data and identifying subtle defects.
False Positive and False Negative Minimization
Balancing sensitivity (avoiding false negatives) with specificity (avoiding false positives) is crucial for an effective automated visual inspection system. A high rate of false positives can lead to unnecessary product rejection, while false negatives can result in the release of defective products.
- Use of statistical process control techniques: Statistical process control techniques can be used to continuously monitor and refine algorithm accuracy.
- Regular algorithm updates: Regular updates to the algorithms are necessary to account for changes in the manufacturing process or variations in product appearance.
- Implementing human-in-the-loop verification: For critical cases, human review and verification can be integrated into the process to minimize the risk of false negatives.
Data Management and Integration
Effective data management and seamless integration with existing quality control systems are essential for compliance and efficient operation. Data generated by the AVI system needs to be securely stored, easily retrievable, and readily accessible for analysis and reporting.
- Need for scalable data storage and retrieval solutions: The volume of data generated by AVI systems requires robust and scalable data storage and retrieval solutions.
- Integration with existing manufacturing execution systems (MES) and enterprise resource planning (ERP) systems: Seamless integration with existing systems ensures efficient data flow and eliminates manual data entry.
- Data analytics for process improvement and predictive maintenance: Data analytics can be used to identify trends, predict potential problems, and continuously improve the manufacturing process.
Regulatory Compliance and Validation
Meeting regulatory requirements is paramount for any pharmaceutical quality control system, and automated visual inspection systems are no exception. Stringent validation and compliance protocols are essential to ensure the system's reliability and data integrity.
Meeting Regulatory Requirements
Automated visual inspection systems for pharmaceuticals must meet stringent regulatory requirements, such as 21 CFR Part 11 in the United States. These regulations address data integrity, audit trails, and user authentication, among other aspects.
- Ensuring data integrity: All data generated by the system must be secure, tamper-proof, and readily auditable.
- Audit trails: Complete audit trails must track all system activities, changes, and user actions.
- User authentication: Robust user authentication mechanisms are required to control access and ensure data security.
- Regular calibration and maintenance: Regular calibration and maintenance are crucial to maintain the system's accuracy and compliance with regulatory standards.
Qualification and Verification of the System
Rigorous testing and validation are crucial to demonstrate the effectiveness of the AVI system. This typically involves a series of qualification steps, including Installation Qualification (IQ), Operational Qualification (OQ), and Performance Qualification (PQ).
- IQ, OQ, and PQ: These qualifications ensure that the system is installed correctly, operates as intended, and performs according to specifications.
- Comparative studies with manual inspection methods: Comparative studies comparing the automated system's performance to traditional manual inspection methods are often required to demonstrate equivalence.
Conclusion
Implementing automated visual inspection for lyophilized drug products presents several significant challenges. However, by addressing the issues of image acquisition, algorithm development, and regulatory compliance, pharmaceutical companies can realize the significant benefits of improved quality control, increased efficiency, and reduced costs. Overcoming these hurdles requires a multifaceted approach involving advanced technologies, robust algorithms, and a commitment to regulatory compliance. Investing in advanced Automated Visual Inspection of Lyophilized Drug Products is an investment in the future of pharmaceutical quality assurance. Don't hesitate to explore the latest advancements in AVI to optimize your lyophilized drug product inspection processes and ensure the highest level of quality and patient safety.
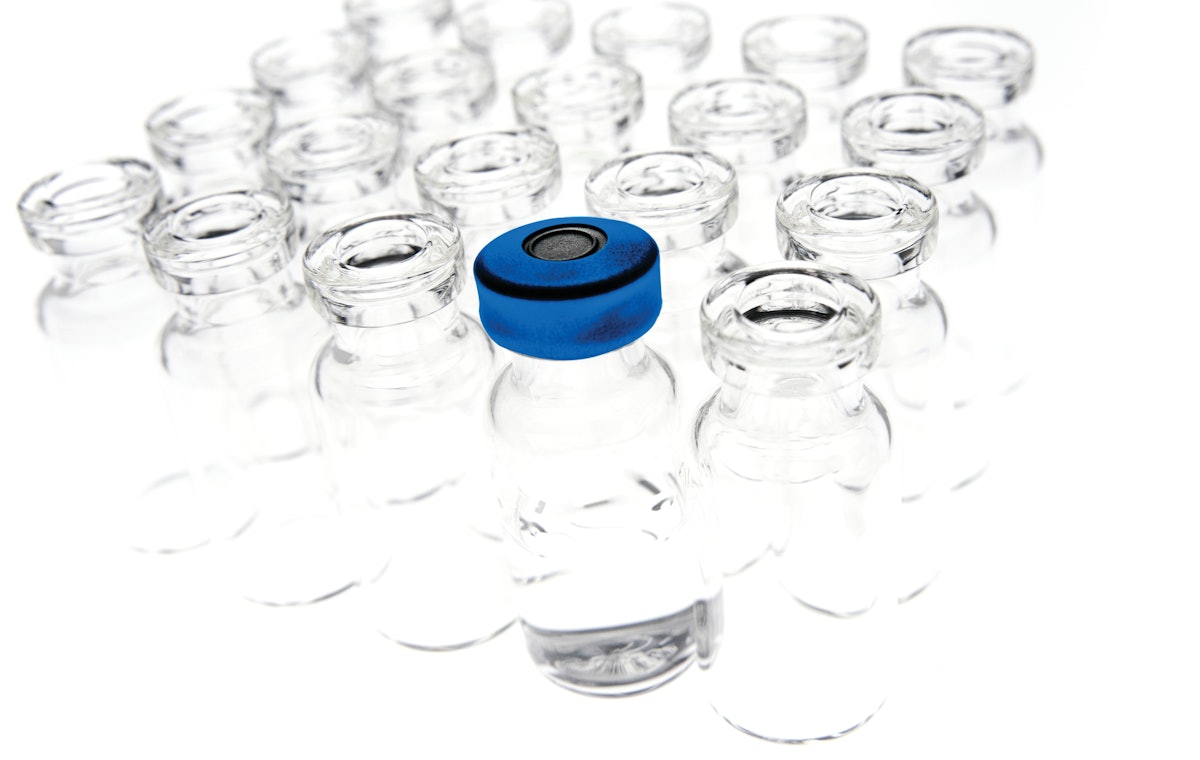
Featured Posts
-
The Internets Buzz A Realistic Fake Captain Britain Trailer With Henry Cavill
May 11, 2025 -
Lily Collins Stars In A New Calvin Klein Campaign See The Photos
May 11, 2025 -
Henry Cavills Superman Future James Gunn Addresses Past Dc Management Decisions
May 11, 2025 -
Everything We Know About The Upcoming Crazy Rich Asians Series
May 11, 2025 -
Before Freaked Exploring Alex Winters Obscure Mtv Sketches
May 11, 2025
Latest Posts
-
Raznoglasiya Dzhonsona I Trampa Po Povodu Reytinga Prezidenta Zelenskogo
May 12, 2025 -
Spor Dzhonsona I Trampa Reyting Zelenskogo 4
May 12, 2025 -
Dzhonson Nazval Nevernymi Utverzhdeniya Trampa O Reytinge Zelenskogo
May 12, 2025 -
Konflikt V Ukraine Dzhonson I Tramp Raznye Podkhody K Mirnym Peregovoram
May 12, 2025 -
Lowry Makes A Move Valspar Championship Contender
May 12, 2025