Reliable Automated Visual Inspection Of Lyophilized Vials: Strategies For Success
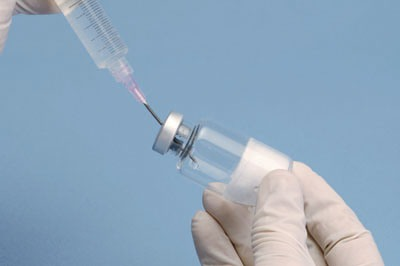
Table of Contents
Selecting the Right Automated Visual Inspection System
Choosing the appropriate automated inspection equipment is the foundation of a successful visual inspection program for lyophilized vials. This decision requires careful consideration of several factors to ensure optimal performance and compliance. The right system leverages advanced image processing and AI in pharmaceutical inspection for superior defect detection.
- Defect Detection Capabilities: Consider the specific types of defects you need to detect. Common defects in lyophilized vials include cracks in the vial, particulate matter within the lyophilized cake, variations in fill level, and label defects. The system should be capable of identifying all relevant defects for your specific product.
- Image Resolution, Speed, and Accuracy: High-resolution imaging is essential for detecting subtle defects. Evaluate systems based on their image resolution, the speed at which they can process vials, and their accuracy in identifying defects. Look for systems with high throughput to keep up with your production demands.
- Compatibility and Flexibility: The chosen system must be compatible with your vial size and format. Consider future scalability; a system that can adapt to changes in vial type or production volume is a valuable long-term investment.
- Robust Software and Data Analysis: Effective data analysis is crucial. Look for systems with user-friendly software that provides detailed reports, facilitates data analysis, and integrates with your existing quality control systems. Powerful machine vision algorithms are essential for accurate and efficient defect identification.
- GMP and Regulatory Compliance: System validation is critical to meet Good Manufacturing Practices (GMP) and other regulatory requirements. Ensure the selected system is validated and provides comprehensive documentation to support compliance.
Optimizing the Inspection Process for Lyophilized Vials
Optimizing the automated visual inspection process for lyophilized vials requires attention to detail and a systematic approach. Careful consideration of several parameters will lead to reliable and accurate defect detection. The goal is to minimize false positives (incorrectly identifying a defect) and false negatives (missing a real defect).
- Lighting Conditions: Proper lighting is crucial for optimal image acquisition. Explore different lighting techniques, such as backlighting and coaxial lighting, to optimize contrast and highlight potential defects within the lyophilized cake. Experimentation may be necessary to find the ideal lighting setup for your specific product and system.
- Clear Acceptance Criteria: Establish clear, well-defined acceptance criteria for different types of defects. This ensures consistency and compliance with regulatory standards. Document these criteria thoroughly.
- Algorithm Optimization: Fine-tuning image processing algorithms is crucial for minimizing both false positives and false negatives. Collaborate with the system vendor to optimize algorithms for your specific product and defect types.
- Rigorous Quality Control: Implement rigorous quality control procedures to validate the accuracy and reliability of the inspection system. This includes regular testing with known good and defective vials.
- Regular Calibration and Maintenance: Regular calibration and preventive maintenance are essential to ensure the continued accuracy and optimal performance of the inspection system.
Handling Challenges Specific to Lyophilized Vials
Lyophilized vials present unique challenges due to the nature of the lyophilization process (freeze-drying). The resulting lyophilized cake can be fragile, and subtle defects can be difficult to detect.
- Cake Fragility: Address the potential challenges related to the inherent fragility of lyophilized cakes. The inspection process must minimize the risk of damage to the vials during inspection.
- Subtle Defect Detection: Develop strategies for detecting subtle defects that may be difficult to identify visually, such as small cracks or partial cake collapse. Advanced imaging techniques can be particularly helpful here.
- Lyophilization Process Variations: Account for variations in the lyophilization process that might impact vial appearance. This may require adjustments to the inspection parameters.
- Advanced Imaging Techniques: Consider advanced imaging techniques, such as 3D imaging or hyperspectral imaging, for improved defect detection, especially for subtle defects within the lyophilized cake. These techniques can provide more comprehensive information than standard 2D imaging.
Data Management and Reporting in Automated Visual Inspection
Data management and reporting are critical for regulatory compliance and process improvement. A robust system ensures data integrity, traceability, and provides valuable insights.
- Data Integrity and Traceability: Implement a robust data management system to ensure data integrity and complete traceability of inspection results. This includes maintaining detailed audit trails.
- Regulatory Compliant Reporting: Generate comprehensive reports that meet all relevant regulatory requirements. Reports should clearly identify defects, their location, and the time of detection.
- Data Analytics for Process Improvement: Utilize data analytics to identify trends and patterns in defect occurrence. This information can be used to improve the lyophilization process and reduce defects.
- Secure Data Storage: Ensure secure storage and access control of all inspection data to maintain confidentiality and regulatory compliance.
Conclusion
Reliable automated visual inspection of lyophilized vials is not merely a best practice; it's a critical requirement for maintaining product quality and ensuring patient safety in the pharmaceutical industry. By carefully selecting and optimizing an automated visual inspection system, addressing the unique challenges posed by lyophilized products, and implementing robust data management procedures, pharmaceutical manufacturers can significantly enhance their quality control processes. Investing in a reliable automated system for visual inspection of lyophilized vials is an investment in patient safety and the long-term success of your pharmaceutical operation. Don't compromise—choose a solution that guarantees the success of your automated visual inspection of lyophilized vials.
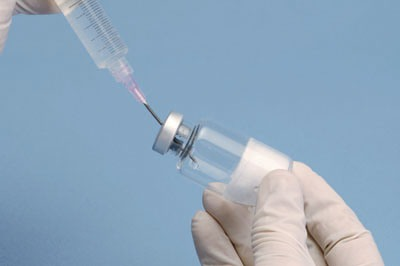
Featured Posts
-
Nine Cardinals In The Running Who Will Be The Next Pope
May 12, 2025 -
Time To Retire John Wick Assessing The Need For A Fifth Film
May 12, 2025 -
2025 Indy 500 Driver Safety Concerns Following Recent Announcement
May 12, 2025 -
Incident U Teksasu Borisa Dzonsona Povredio Noj
May 12, 2025 -
Stellantis Ceo Decision Imminent Us Head A Leading Candidate
May 12, 2025
Latest Posts
-
Two Sides Of The Coin A Look At Sylvester Stallone And Michael Caines Contrasting On Screen Dynamics
May 12, 2025 -
Netherlands Addresses Asylum Challenges Low Security Centers And Area Bans
May 12, 2025 -
New Approach Netherlands Response To Asylum Seeker Challenges With Controlled Detention And Area Restrictions
May 12, 2025 -
Marjolein Fabers Ribbon Gate Inspires Kings Day Mural At Amsterdam Cafe
May 12, 2025 -
The Unexpected Duo Exploring Stallone And Caines Diverse Film Collaborations
May 12, 2025