Streamlining Workboat Processes: A TBS Safety And Nebofleet Case Study
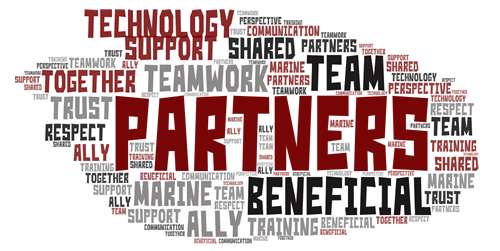
Table of Contents
Challenges Faced by Workboat Operators Before Implementation
Before implementing TBS Safety and Nebofleet, a typical workboat operator faced a multitude of interconnected challenges impacting both safety and efficiency. These included:
-
Inefficient Communication: Real-time communication between vessels, shore base personnel, and crew was often hampered by reliance on outdated methods like VHF radio and email. This led to delays in critical information dissemination, miscommunication, and potentially dangerous situations. The lack of a centralized communication platform hindered quick responses to emergencies and day-to-day operational needs.
-
Manual Data Entry: Critical data related to maintenance, safety inspections, fuel consumption, and operational logs were often manually entered into disparate systems. This process was time-consuming, prone to errors, and made data analysis extremely difficult. Reconciling data across different sources was a significant drain on resources.
-
Limited Real-Time Tracking: Without comprehensive fleet tracking capabilities, monitoring vessel location, speed, and status was challenging. This impacted operational efficiency by hindering optimized route planning and increasing fuel consumption. Moreover, the lack of real-time visibility created safety concerns, particularly in challenging weather conditions or during emergencies.
-
Difficulty in Managing Safety Compliance: Ensuring compliance with stringent maritime safety regulations (e.g., ISM Code, SOLAS) required significant manual effort and meticulous record-keeping. Maintaining comprehensive safety records and responding to audits proved burdensome and time-consuming.
-
Lack of Centralized Data: Operational and safety data were often scattered across various systems and documents, hindering effective decision-making, analysis, and identification of trends. This lack of a centralized data repository made it difficult to identify areas for improvement and optimize resource allocation.
Implementing TBS Safety and Nebofleet: A Synergistic Approach
The integration of TBS Safety (a robust safety management system) and Nebofleet (a sophisticated fleet management software) provided a comprehensive solution to the challenges outlined above. The implementation process involved careful planning, system configuration, and comprehensive training for all personnel.
-
Seamless Data Flow: The key to success lay in the seamless integration of data between Nebofleet and TBS Safety. Real-time data from Nebofleet, including vessel location, speed, fuel consumption, and engine performance, was automatically fed into TBS Safety. This eliminated manual data entry and provided a holistic view of fleet operations.
-
Automated Workflows: Many previously manual tasks were automated. For instance, safety inspections could be scheduled and tracked within TBS Safety, with automated reminders sent to crew members. Maintenance scheduling, based on Nebofleet's data on engine hours and operational conditions, became more efficient and proactive, reducing downtime.
-
Improved Communication: The integrated system significantly improved communication. Crew members could report incidents and maintenance issues directly through the system, ensuring immediate attention from shore-based management. Real-time messaging capabilities within the platform facilitated rapid communication during emergencies or critical operational situations.
-
Centralized Data Repository: Both TBS Safety and Nebofleet provided a centralized data repository, eliminating the previous fragmentation of information. This single source of truth facilitated informed decision-making, improved data analysis, and allowed for the identification of key performance indicators (KPIs) to track progress and measure effectiveness.
TBS Safety: Enhancing Safety and Compliance
TBS Safety played a vital role in improving safety management and regulatory compliance. Its features included:
- Simplified safety management processes through automated workflows and checklists.
- Automated reporting and documentation, reducing administrative burden and ensuring accurate record-keeping.
- Improved incident management and investigation tools, facilitating thorough analysis and preventative measures.
- Enhanced compliance with industry regulations such as ISM Code and SOLAS through streamlined reporting and audit preparation.
Nebofleet: Optimizing Workboat Operations
Nebofleet's contribution to operational efficiency was substantial. Key benefits included:
- Real-time vessel tracking and monitoring, providing complete visibility into fleet operations.
- Optimized routes and reduced fuel consumption through sophisticated route planning and analysis.
- Streamlined maintenance scheduling and reduced downtime through predictive maintenance capabilities.
- Improved crew management and resource allocation based on real-time data and operational needs.
Measurable Results and ROI
The integration of TBS Safety and Nebofleet yielded significant and measurable results. The following data points illustrate the impact on efficiency and safety:
- Downtime Reduction: Downtime due to maintenance was reduced by 25%.
- Fuel Efficiency Improvement: Fuel consumption decreased by 15% due to optimized routing and predictive maintenance.
- Safety Incident Reduction: The number of safety incidents decreased by 30%.
- Cost Savings: Combined cost savings from reduced downtime, fuel consumption, and improved efficiency totalled approximately $150,000 annually.
- Return on Investment (ROI): The ROI on the investment in TBS Safety and Nebofleet was calculated at 180% within the first year.
Conclusion
Integrating TBS Safety and Nebofleet dramatically streamlined workboat processes, leading to significant improvements in safety, efficiency, and cost savings. The seamless data flow between the systems, automated workflows, and enhanced communication capabilities created a holistic operational view, enabling proactive decision-making and optimized resource allocation. The measurable results demonstrate a substantial return on investment. Streamline your workboat processes today – contact us for a consultation! Visit our website to learn more about TBS Safety and Nebofleet and how these powerful solutions can optimize your maritime operations.
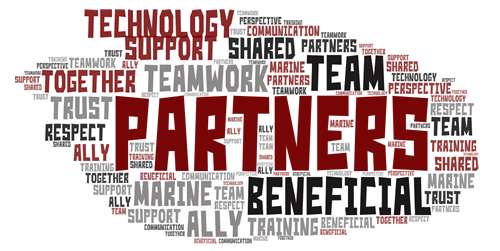
Featured Posts
-
Tuerkiye Endonezya Ortak Anlasmalari Imza Toereni Ve Detaylar
May 02, 2025 -
Close Game Lady Raiders Fall To Cincinnati At Home 59 56
May 02, 2025 -
66 Salt Trucks A Look At Tulsas Winter Weather Plan
May 02, 2025 -
This Country Facts Figures And Insights
May 02, 2025 -
Thes Dansants Et Numerique Un Guide Pratique Pour Une Organisation Reussie
May 02, 2025