The Future Of Automated Visual Inspection For Lyophilized Vials: Tackling Current Limitations
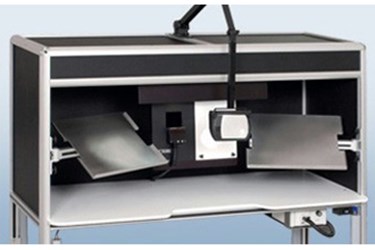
Table of Contents
Current Limitations of Automated Visual Inspection in Lyophilized Vial Inspection
Automated visual inspection of lyophilized vials is essential, yet existing systems struggle with several key limitations that impact efficiency and product quality.
Challenges in Defect Detection
Identifying defects in lyophilized vials presents unique difficulties. The porous nature of the lyophilized cake, coupled with the often-subtle nature of defects, makes automated detection challenging.
- Subtle Defects: Cracks in the lyophilized cake, small particulate matter, and inconsistencies in fill level are difficult to distinguish against the background of the freeze-dried product. Current 2D imaging often struggles to capture these three-dimensional variations.
- Lyophilization Process Variability: Variations in the lyophilization process—including sublimation rate, temperature, and pressure—can significantly alter the appearance of the final product. This variability leads to increased false positives, where non-defective vials are incorrectly flagged.
- Limitations of 2D Imaging: Traditional 2D imaging systems struggle with detecting three-dimensional defects. A crack that might be easily visible in a 3D view can be missed in a 2D image. This limitation necessitates further investigation and manual intervention.
- Impact on Production: These challenges directly impact production efficiency, increasing inspection times and costs while potentially releasing sub-standard products. The consequences of releasing defective vials can be severe, leading to product recalls and reputational damage.
High False Positive Rates and Their Consequences
A major limitation of current AVI systems is the high rate of false positives. This means that many vials are flagged as defective when they are, in fact, perfectly acceptable.
- Manual Verification Bottleneck: This necessitates manual intervention to verify each flagged vial, creating a significant bottleneck in the inspection process. This manual review is time-consuming, costly, and introduces the risk of human error.
- Resource Intensive: The time and resources dedicated to manual inspection significantly impact overall production efficiency and profitability. This includes the labor costs, the potential for delays in release, and the added strain on quality control personnel.
- Human Error Risk: Manual inspection is susceptible to human error, leading to potentially defective vials being released into the market. This underscores the critical need for more accurate and automated systems.
Emerging Technologies for Enhanced Automated Visual Inspection
Fortunately, several emerging technologies offer significant improvements in the automated visual inspection of lyophilized vials.
Advanced Imaging Techniques
The limitations of traditional 2D imaging are being overcome by advanced imaging technologies.
- 3D Imaging: Techniques like structured light and confocal microscopy provide three-dimensional views of the vials, enabling the detection of subtle defects that are invisible to 2D systems. This allows for more comprehensive and accurate inspection.
- Hyperspectral Imaging: This technique captures information across a wide range of wavelengths, providing detailed spectral information about the vial contents. This allows for the detection of subtle variations in material properties that might indicate defects, even if visually undetectable.
- Artificial Intelligence (AI) and Machine Learning (ML): AI and ML algorithms can be trained to recognize patterns associated with defects, significantly improving the accuracy of defect detection and reducing false positives. These algorithms continuously learn and adapt, improving performance over time.
Improved Data Analysis and Algorithm Development
Sophisticated algorithms and data analysis are crucial for maximizing the effectiveness of advanced imaging techniques.
- Advanced Algorithms: The development of more robust algorithms is crucial for accurately identifying and classifying defects. These algorithms can analyze complex image data and differentiate between true defects and variations in the lyophilization process.
- Data Integration: Integrating data from various sources—such as process parameters (e.g., temperature, pressure), spectral data from hyperspectral imaging, and image data from 3D imaging—can provide a more complete picture of the vial's quality.
- Robust Statistical Methods: Statistical methods are critical for managing the inherent variability in the lyophilization process and minimizing the impact of this variability on the inspection results.
Future Trends and Predictions for Automated Visual Inspection of Lyophilized Vials
The future of automated visual inspection of lyophilized vials is bright, with several key trends shaping the field.
Increased Automation and Integration
The trend is towards fully automated inspection lines, minimizing manual intervention and maximizing efficiency.
- Fully Automated Lines: Future systems will seamlessly integrate all aspects of the inspection process, from vial handling to defect classification and reporting. This reduces the risk of human error and increases throughput.
- Process Analytical Technology (PAT) Integration: Integrating AVI systems with other PAT tools will allow for real-time quality control, enabling immediate adjustments to the lyophilization process based on inspection results. This proactive approach minimizes waste and improves product quality.
Enhanced Regulatory Compliance
Advanced AVI systems play a crucial role in meeting stringent regulatory requirements.
- Comprehensive Audit Trails: These systems provide detailed audit trails, documenting every step of the inspection process. This ensures compliance with regulatory guidelines and facilitates efficient investigations in case of issues.
- Data Integrity: Robust data management and secure data storage are vital for maintaining data integrity, a crucial aspect of regulatory compliance.
Cost-Effectiveness and ROI
While the initial investment in advanced AVI systems may be higher, the long-term cost savings are significant.
- Reduced Manual Labor: Minimizing manual inspection significantly reduces labor costs.
- Improved Efficiency: Faster inspection times and reduced downtime lead to increased production efficiency and faster time-to-market.
- Minimized Product Waste: Accurate defect detection reduces the risk of releasing defective products, minimizing waste and associated costs.
Conclusion: The Future of Automated Visual Inspection for Lyophilized Vials
Current automated visual inspection systems for lyophilized vials face significant challenges in detecting subtle defects and managing high false-positive rates. However, emerging technologies such as advanced 3D imaging, hyperspectral imaging, AI, and sophisticated algorithms offer a path towards overcoming these limitations. Investing in advanced automated visual inspection of lyophilized vials is crucial for ensuring product quality, meeting stringent regulatory requirements, and achieving long-term cost-effectiveness. Invest in the future of pharmaceutical quality control by exploring the latest advancements in automated visual inspection of lyophilized vials. Contact us today to learn more!
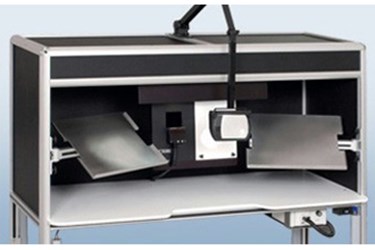
Featured Posts
-
Saisonende Bundesliga Abstieg Fuer Bochum Und Holstein Kiel Leipzig Ohne Champions League
May 12, 2025 -
National Fallen Firefighters Memorial Tribute To Fremonts Wolf River Firefighter
May 12, 2025 -
Apples Dependence On Google A Strategic Analysis
May 12, 2025 -
Injury Updates Yankees Vs Brewers Series March 27 30
May 12, 2025 -
New Calvin Klein Campaign Featuring Lily Collins Photo Gallery
May 12, 2025
Latest Posts
-
Stricter Border Security A Shift Towards Prevention Over Apprehension
May 12, 2025 -
Increased Border Checks Lead To Fewer Arrests More Deportations
May 12, 2025 -
Asylum Policy Under Fire Ministers Dismissal Of Inspectorate Opinion
May 12, 2025 -
Fewer Arrested More Turned Away The Rise Of Stricter Border Controls
May 12, 2025 -
Controversy Asylum Minister Bypasses Legal Advice From Inspectorate
May 12, 2025