Trump Tariff Impact: Navigating The Challenges For Automakers
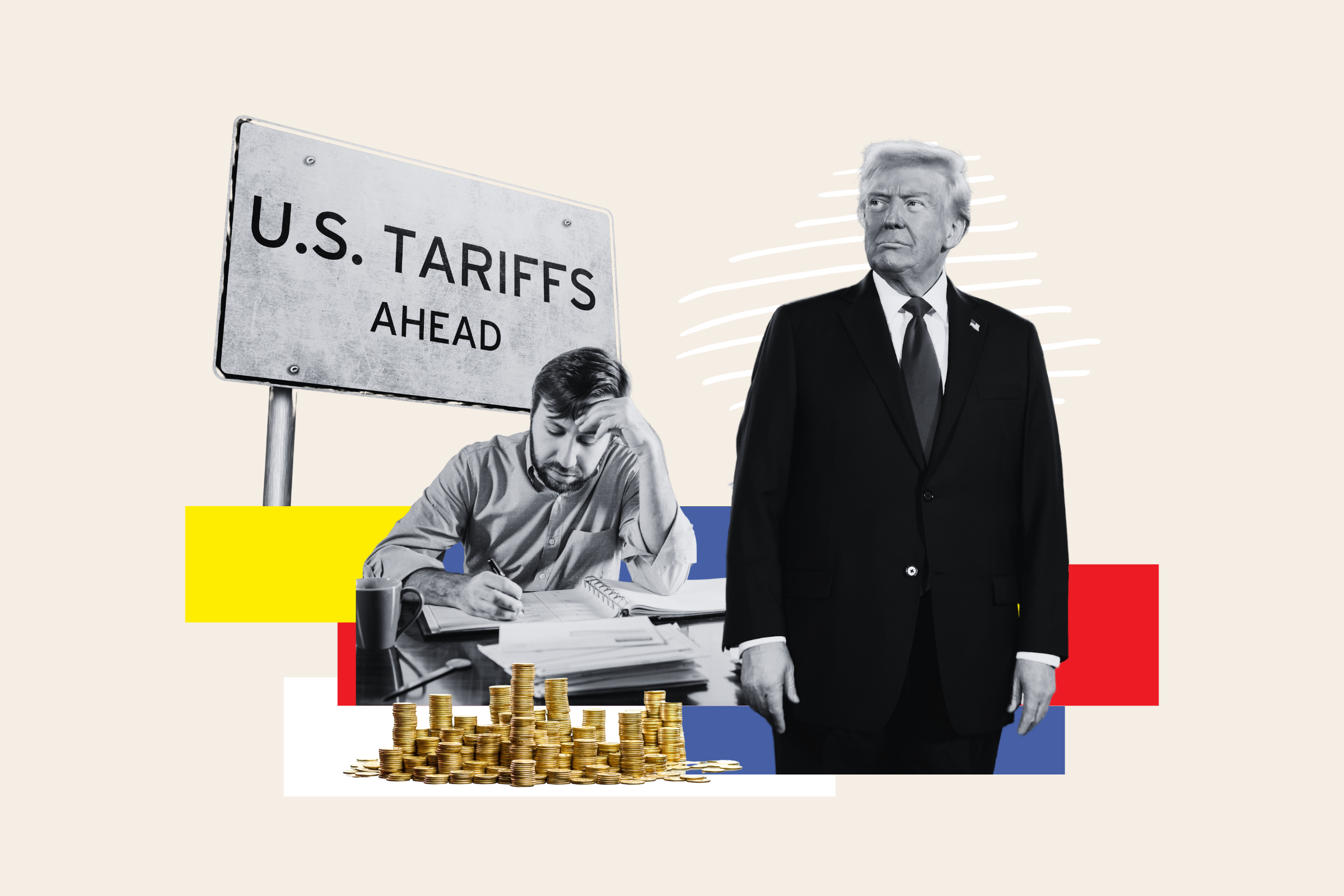
Table of Contents
Increased Production Costs and Reduced Profit Margins
The Trump tariffs, particularly those targeting steel, aluminum, and various auto parts, directly increased manufacturing costs for automakers. Tariffs on imported steel, for instance, added significantly to the cost of producing car bodies and chassis. Similarly, tariffs on imported components, ranging from electronics to specialized machinery, inflated the overall price of manufacturing vehicles.
For example, the 25% tariff on imported steel added thousands of dollars to the production cost of certain popular pickup trucks, impacting profit margins significantly. This pressure on profit margins forced automakers to consider several difficult options: absorb the increased costs, raise vehicle prices for consumers, or reduce production.
- Higher input costs for raw materials: Tariffs on steel and aluminum dramatically increased the cost of essential raw materials.
- Increased cost of imported components: Tariffs on imported parts like electronics, engines, and transmissions added to the manufacturing expense.
- Reduced competitiveness in global markets: Higher production costs reduced the price competitiveness of American-made vehicles in international markets.
- Potential for job losses due to decreased production: Some automakers responded to reduced profitability by decreasing production, leading to potential job losses.
Disrupted Supply Chains and Production Delays
Relying on intricate global supply chains became extremely problematic under the Trump tariffs. The imposition of tariffs forced many automakers to reconsider their sourcing strategies, often leading them to seek more expensive domestic alternatives. This shift not only increased costs but also introduced considerable delays. Finding reliable domestic suppliers capable of meeting the same volume and quality standards as established international suppliers proved difficult and time-consuming.
- Finding alternative suppliers: The search for new suppliers often resulted in delays and disruptions to the supply chain.
- Increased lead times for components: New suppliers frequently had longer lead times, causing production bottlenecks.
- Production bottlenecks and delays: Shortages of specific parts due to supply chain disruptions halted production lines.
- Inventory management challenges: Automakers faced significant challenges in managing inventory levels to account for unpredictable delays and fluctuating supply.
Impact on Consumer Demand and Market Share
The increased cost of vehicles, a direct result of the tariffs, inevitably impacted consumer demand. Higher prices reduced affordability for many potential buyers, leading to decreased sales volumes for several automakers. Furthermore, this price increase made American-made vehicles less competitive against foreign brands that were less affected by these tariffs.
- Reduced consumer affordability: Higher vehicle prices due to tariffs dampened consumer demand.
- Loss of market share to foreign competitors: Foreign automakers, unaffected by the tariffs, gained a competitive edge.
- Potential for decreased sales volume: Reduced consumer demand translated to lower sales figures for many domestic automakers.
- Impact on the overall economic health of the automotive sector: The ripple effect of decreased sales and production affected the overall health of the automotive sector.
Strategies for Automakers to Mitigate Tariff Challenges
To offset the negative impacts of the Trump tariffs, automakers employed various strategies. Some chose to relocate production facilities to countries with more favorable trade agreements (nearshoring or reshoring), others focused on diversifying their supplier base to reduce reliance on any single source, while some invested heavily in automation and technology to increase efficiency and reduce reliance on imported parts. Simultaneously, industry lobbying efforts played a crucial role in advocating for tariff reductions or exemptions.
- Reshoring or nearshoring production: Relocating manufacturing to reduce reliance on tariff-affected imports.
- Supplier diversification and negotiation: Developing multiple supply chains to mitigate the risk of disruptions.
- Investing in automation and technology: Improving efficiency to compensate for increased costs.
- Lobbying efforts for policy changes: Advocating for tariff reductions or exemptions to alleviate pressure.
Conclusion: Navigating the Future with Trump Tariff Lessons Learned
The Trump tariff impact on automakers was multifaceted and significant, leading to increased production costs, disrupted supply chains, and decreased consumer demand. However, the response of automakers demonstrated the importance of strategic adaptation. By diversifying sourcing, investing in automation, and engaging in active lobbying, companies navigated these challenges, though often at a considerable cost. Understanding the Trump tariff impact is crucial for automakers. Staying informed on evolving trade policies and proactively developing flexible strategies is essential to effectively navigate future challenges. Further research into the long-term effects of these trade policies on global supply chains and the automotive industry is vital for future preparedness.
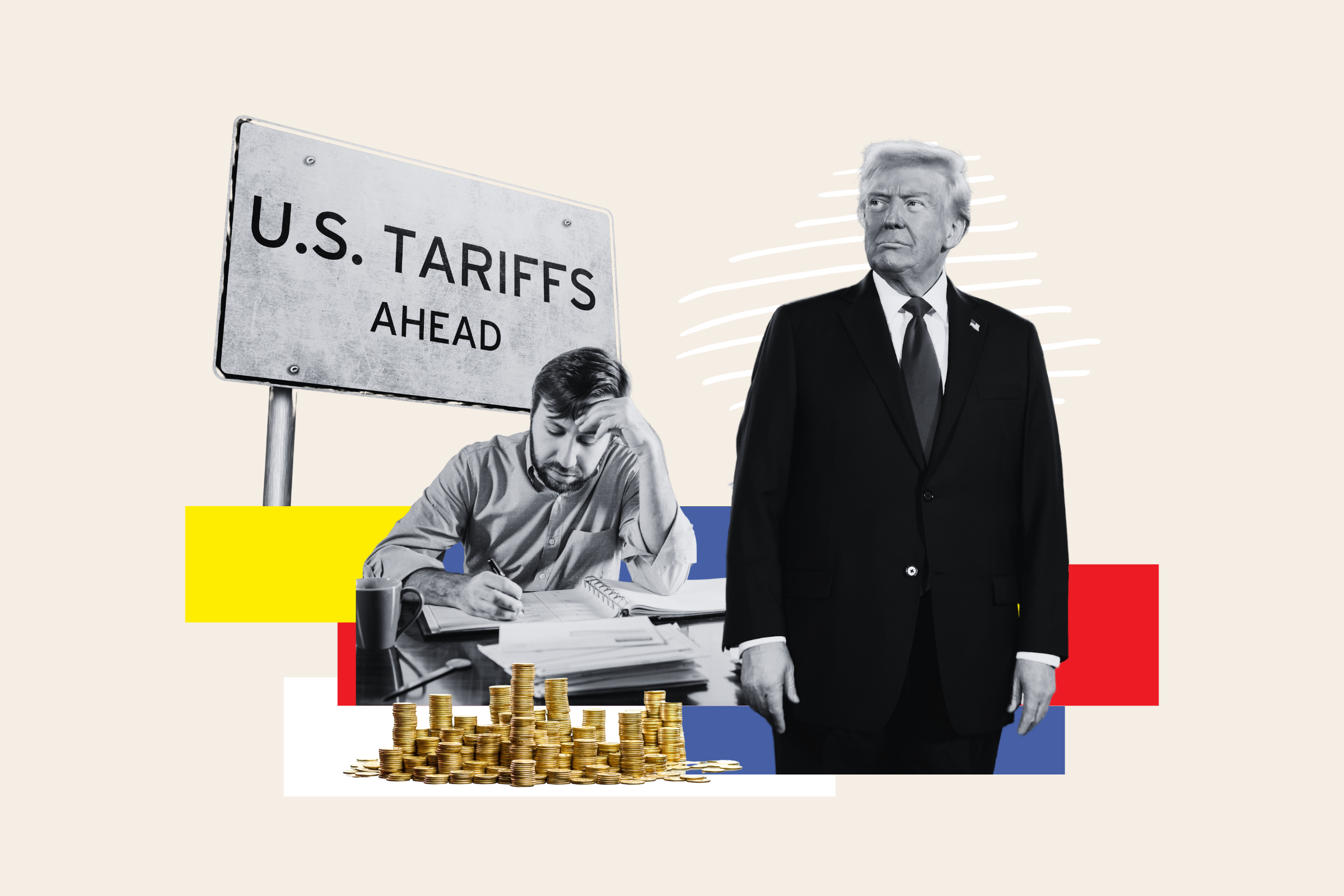
Featured Posts
-
Promoting Mental Wellness 5 Practical Steps For Community Acceptance
May 02, 2025 -
Reduced Sec Settlement The Future Of Xrp And Ripples Next Steps
May 02, 2025 -
Broadcoms Proposed V Mware Price Increase At And T Details A 1050 Jump
May 02, 2025 -
Former Uk Official Rupert Lowe Reported To Police For Bullying
May 02, 2025 -
Mqbwdh Kshmyr Agha Syd Rwh Allh Mhdy Ky Bharty Palysy Pr Tnqyd
May 02, 2025